Behind-the-Scenes: How a Spreader is Made
Created January 18, 2023
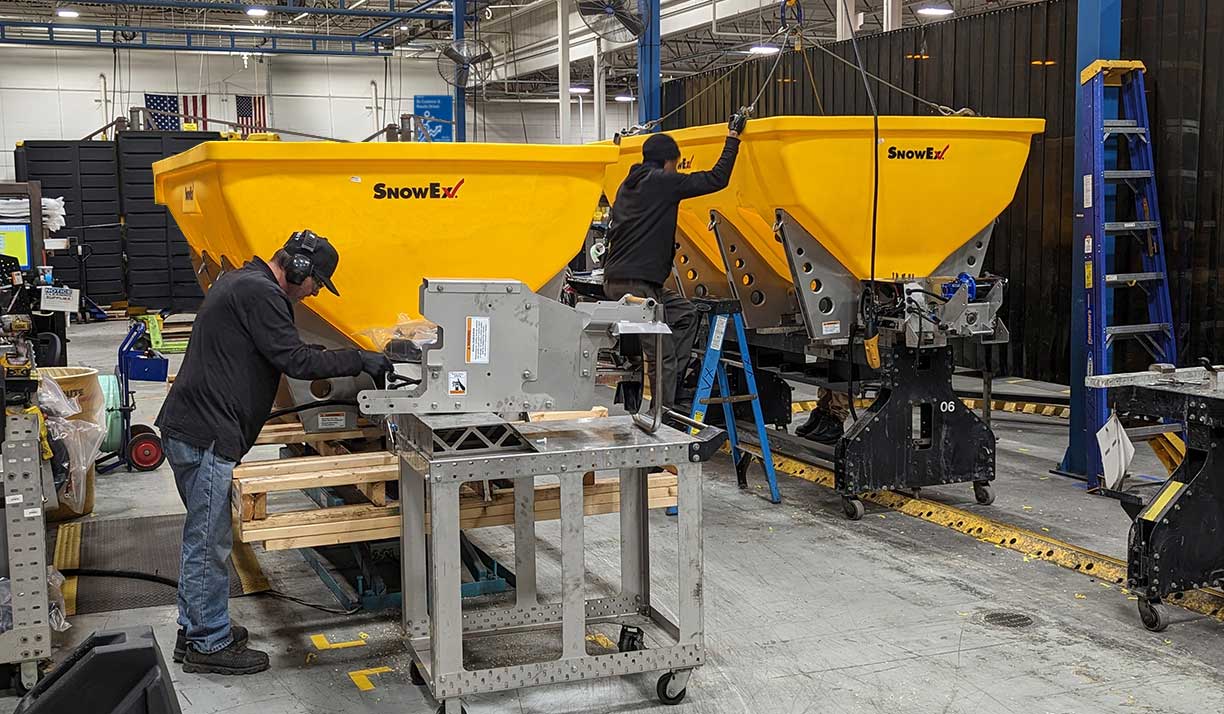
Since 1997, SnowEx® has been the leader in ice control, known for having a wide variety of spreaders and liquid solutions. We’re bringing you behind-the-scenes to explain the process a spreader goes through from concept to complete product.
Product Concepts That Meet Contractor Needs
New spreader concepts can come from anywhere, sometimes even our most loyal customers. Contractors know the products inside and out, work in the elements, and depend on SnowEx products to service their client’s properties. They are the best candidates to highlight additional product needs and drive the innovations that can help transform the industry.
Once our marketing teams collect information from contractors, dealers, and the overall industry—our engineering team gets to work designing products that convert our various customer needs into tangible, unique solutions that strengthen our product lines.
Developing the Groundwork & Cross-Functional team
The foundation for new product development usually begins with in-depth market studies, cost analysis, and a business case to get buy-in before launching a cross-functional team for design and engineering work.
These teams look at what’s been done in the past and audit similar product lines. They determine the core user of the equipment, what their needs are, and any regulation standards or real-world parameters that need to be considered. For instance, standard sidewalk widths should be taken into account if you’re designing equipment for sidewalk snow and ice maintenance.
Key stakeholders are brought in early in the process to make sure all necessary perspectives are taken into consideration.
Designing & Constructing the First Prototype
Once the team understands the market need and the project is approved, we get to work on a 3D CAD design model. After we have a CAD model, we can make a small-scale prototype model. This process has advanced over the years with the recent development of 3D printing technology.
What was once technical specifications on paper can now be brought to life in a physical form. Today, we can take a complete 8-foot spreader and scale it down to a 3D printed, 8-inch version to get a visual representation of what the product will be before building it to scale. This helps jumpstart the internal buy-in process where core team leads from engineering, marketing, manufacturing, and other key stakeholders can start to review aesthetic design and construction. They can touch it, feel it, open it up and see how the moving parts will function.
By adding this step to our process, we’ve been able to highlight potential problems earlier in the process so we can quickly pivot and implement alternative solutions. We try to gain as much input as possible early in the process to ensure that we have quality product that meets our strict standards.
Rigorous Testing
We start with computer simulations and component lab testing to replicate real-world effects for testing new products. These tools allow us to gain high levels of confidence with the design, before manufacturing the first part.
Then we bring in our technical service department to evaluate the design for ease of installation, servicing, and maintenance. Their extensive technical experience and knowledge is incredibly beneficial at this stage of development—not only do we want our products to perform well, but we also want to ensure the installation and maintenance processes go smoothly. This includes owner’s manuals, installation instructions, and parts lists for future service needs.
Lastly, we perform field testing at the full assembly level with experienced testers that try to push the product to its limits. This provides real world feedback that can help us redesign to further strengthen the product before we begin manufacturing.
On the Shop Floor
Our lean manufacturing production process leverages historical production rhythms and in-house laser and press brakes to maximize yield and minimize waste—especially with higher volume units. While it usually depends on design complexity and the number of units forecasted, manufacturing a spreader typically demands a multi-person, multi-robot assembly line.
We level load our production line depending on product popularity and complexity of the design and build to ensure we can meet demand. We are always working towards continuous improvement, finding more efficient ways to manufacture and deliver products to our customers faster.
A Legacy of Innovation
At SnowEx, we take pride in pushing the envelope on product innovation and are committed to providing our customers with a superior experience. The voice of contractors has helped us shape and evolve our products over time and has transformed more than just our product offerings. Industry feedback has also improved our industry-leading guarantee where SnowEx was the first to offer a 2-year Parts & Labor Warranty on all equipment.
You’ve dedicated your career to snow and ice management. That’s why we listen to what you have to say—Because no one knows what it takes better than you.